|
Q: What is the difference between contact cleaning and non-contact cleaning?
A: Non-contact systems are unable to defeat the boundary layer created by moving material. For more information on the boundary layer, please click here.
Q: Why choose contact cleaning?
A: Contact cleaning offers a higher efficiency cleaning system. Non-contact systems are limited to cleaning particles down to around 20 microns. In some application such as reel-to-reel, the web creates an air barrier as it moves. Non-contact systems cannot pierce the air barrier, which greatly limits the cleaning ability of these systems. Contact cleaning breaks this barrier and allows for optimal cleaning.
Back to Top
Q: What is tacky-roller or polymer roller cleaning?
A: Tacky-roller or polymer roller cleaning is a specific type of contact cleaning. In these systems, a polymer roller creates a nip through which the material being cleaned passes. As the material passes through the nip, the contamination is lifted by the tackiness of the polymer roller. The polymer roller subsequently runs against an adhesive coated roll and passes the contamination to the adhesive roll, permanently trapping the dirt on the adhesive. The adhesive roll is reverse wound. Therefore, when the surface of the adhesive is fully loaded with contamination, the roll is simply unwound one revolution and cut, thus providing a fresh adhesive surface in contact with the elastomer roller. One big advantage is that tacky roller systems are free of liquid so they can be employed prior to critical steps (printing, coating, laminating, etc.) where liquid is not allowed.
Back to Top
Q: Is tacky-roller or polymer roller cleaning the best for all applications?
A: Tacky-roller or polymer roller will remove more contamination than non-contact cleaning. Dust (including lint, hair, clothing fibres and other airborne contamination) on a substrate can only be removed by moving air down as far as the “boundary layer”. This is a very thin layer immediately adjacent to the surface where air velocity is significantly reduced, dramatically reducing the cleaning ability of moving air. Consider a dusty TV screen – blowing on it (non-contact) will not remove all the contamination, it will normally require a soft cloth (contact) to clean it properly. More information on the boundary layer can be found on this NASA web page.
Back to Top
Q: Which should I use, a vacuum or polymer roller system?
A: A vacuum is good for large particles and heavy contamination (typically low-tech environments). A vacuum will struggle to remove particles less than 100 microns in diameter.
Polymer rollers (also known as elastomer, rubber or tacky rollers) are better for small particles and light contamination (typically high tech environments). They can remove particles less than 1 micron in size, and transfer them safely to a co-rotating adhesive roll which stores the contamination away from the substrate.
Back to Top
Q: How long does the adhesive roll last? How often will I need to change it?
A: The adhesive roll, like any receptacle for contamination, fills up more quickly when more contamination is available. Just as a family of four will create more waste than a single person, a heavily contaminated or very fast moving substrate will have more dust to transfer than one lightly contaminated or moving slowly. The quicker it is used, the more work it is doing.
Back to Top
Q: What is the polymer roller made of?
A: Many formulations contain silicone, which gives excellent cleaning qualities, but may be unsuitable for certain applications, such as in printed circuit board production, or on glass – here we would supply silicone-free polymers which give exactly the same cleaning qualities.
Back to Top
Q: Are all the polymer rollers the same?
A: SDI lead the market in polymer formulations. Rather than a “one size fits all” policy, we examine each customer application carefully to ensure that the correct polymer is used to give the best combination of cleaning ability and processability. For example, a very aggressive polymer will clean well, but is unsuitable for very thin and delicate substrates, so is best used for rigid products.
Back to Top
Q: Do the rollers remove static?
A: No. Any static-sensitive substrate moving against or between rollers will be charged by the contact. SDI machines offer an anti-static system to remove static from a substrate after cleaning, so that it is not attracting airborne contamination to the freshly cleaned surface.
Back to Top
Q: How long do the polymer rollers last?
A: Again, this is very dependent on the application. Used 24/7, the cleaning ability of the roller will diminish more quickly than one used occasionally, though all rollers will retain a level of cleaning performance, no matter how old. Compare the roller to the tires on a car, new ones will hold the road better, and high-mileage drivers will change them regularly. Older tires do not have the same performance, but will still get the driver from A to B.
Back to Top
Q: What if silicone is not allowed in my production line?
A: SDI is the only supplier that can provide a proven system that is completely silicone-free. Other suppliers have been telling their customers for years that the rollers contain no silicone. SDI chooses to solve the problem instead of pretending the problem does not exist.
Back to Top
Q: What if my application is too dirty for tacky, vacuum is not enough, and liquids are not allowed?
A: SDI has created the first rotary/vacuum system for just such application. The unit combines the large collection capacity of vacuum and the benefits of contact cleaning. The system requires only vacuum and shop air.
Back to Top
|
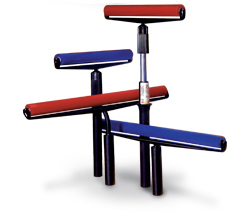 |
21 Morgan, Irvine, CA 92618
949.583.1001 phone
949.583.7007 fax |
|